goodbye to noise, hello to higher yield
Flowsonic Use Case
Thanks to the flowsonic® ultrasonic discharge and dosing aid from Artech Ultrasonic Systems, the long-established Swiss company Nahrin is able to reduce noise pollution for employees considerably. Furthermore, the capacity of the filling line for Nahrin’s natural and tasty seasonings is increased by over 30%.
Date
April 2024Customer Location
Nahrin AG, Sarnen, SwitzerlandProduct
SeasoningsTask
Discharge aid from two dosing hoppers
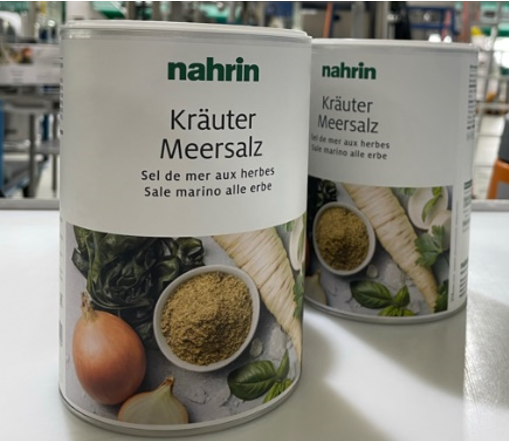
Initial situation / Problem
The dosing system of the natural ingredients specialist in the heart of Switzerland consists of two conical collecting and dosing units, among other things. First, the spice mixtures are conveyed into the first hopper (application A) by means of a dosing feeder.
The product then reaches the filling station, where a dosing hopper (application B) fills the specified quantities into the tins. In both applications, there were regular discharge problems as the product compacted above the outlets. This repeatedly led to bridging, which could only be broken up using mechanical vibrators and manual hammer blows (Fig. 1).
The product then reaches the filling station, where a dosing hopper (application B) fills the specified quantities into the tins. In both applications, there were regular discharge problems as the product compacted above the outlets. This repeatedly led to bridging, which could only be broken up using mechanical vibrators and manual hammer blows (Fig. 1).
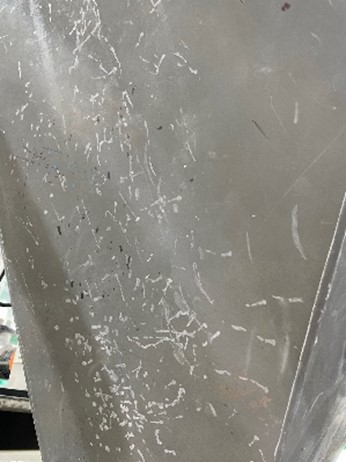
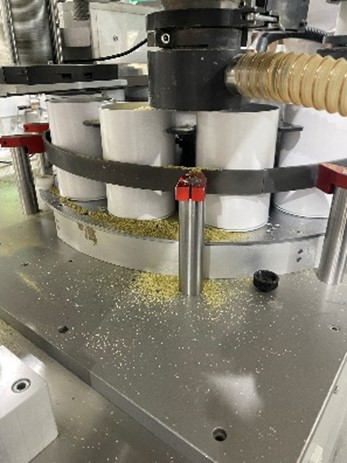
This caused problems throughout the entire dosing process. On the one hand, the employees were constantly exposed to increased noise pollution (over 90dB) caused by the knockers.
On the other hand, the irregular, abrupt dosing caused by the mechanical flow aids meant that Nahrin's strict quality specifications regarding filling quantities could not be met in some cases. As a result, some of the affected cans had to be refilled. In addition, valuable product was lost during the process (Fig. 2)
On the other hand, the irregular, abrupt dosing caused by the mechanical flow aids meant that Nahrin's strict quality specifications regarding filling quantities could not be met in some cases. As a result, some of the affected cans had to be refilled. In addition, valuable product was lost during the process (Fig. 2)
Approach
Thanks to close cooperation between the customer and Artech, mechanical waveguides made of aluminum were developed specifically for this project. These were welded to the outer walls of the two hoppers.
The ultrasonic converters were then screwed on (Fig. 3). The ultrasonic generator (Fig. 4) was used to analyse the frequencies of the applications and parameterize jobs.
The ultrasonic converters were then screwed on (Fig. 3). The ultrasonic generator (Fig. 4) was used to analyse the frequencies of the applications and parameterize jobs.
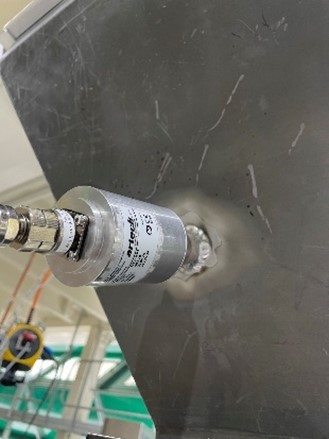
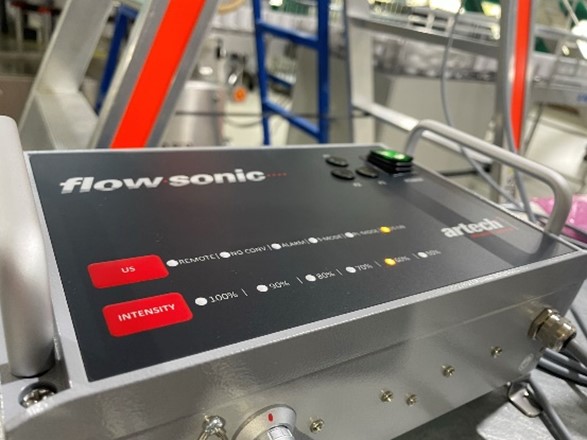
Results / Advantages
By using the Artech ultrasonic discharge and dosing aid flowsonic®, mechanical vibrators and manual hammer blows can now be completely avoided.
Noise pollution has been significantly reduced from the original level of over 90dB.
In addition to the noise reduction, the optimized dosing within the quantity tolerances enables employees carry out less heavy work, such as transporting and emptying cans back into the hopper.
In addition to more precise dosing and correspondingly less waste (Fig. 5), the average dosing time per can has been improved by approx. 30% thanks to the smooth powder flow (Fig. 6) (example seasoning mix 730 grams = standard dosing time per unit: without ultrasound 2.2 seconds, with ultrasound 1.5 seconds).
Noise pollution has been significantly reduced from the original level of over 90dB.
In addition to the noise reduction, the optimized dosing within the quantity tolerances enables employees carry out less heavy work, such as transporting and emptying cans back into the hopper.
In addition to more precise dosing and correspondingly less waste (Fig. 5), the average dosing time per can has been improved by approx. 30% thanks to the smooth powder flow (Fig. 6) (example seasoning mix 730 grams = standard dosing time per unit: without ultrasound 2.2 seconds, with ultrasound 1.5 seconds).
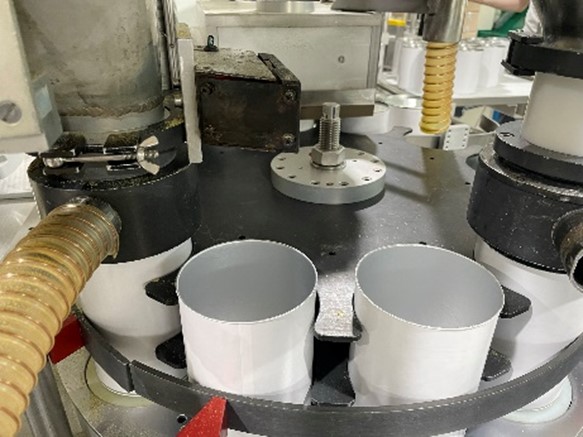
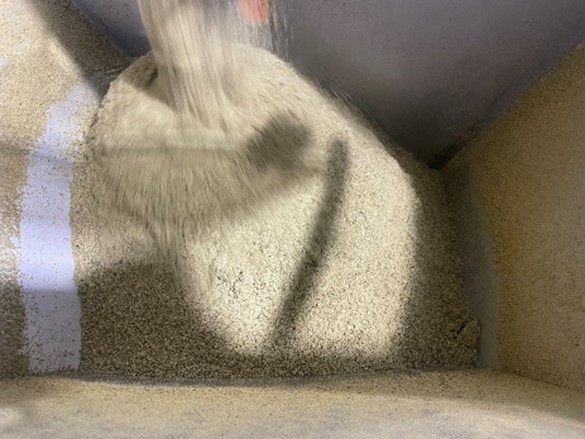
Ready to get started?
Our expert team willl help deliver your next project on-time, within budget and the the exacting standards you would expect.
Contact UsBook a Call