Ultrasonic welding is one of the most economical and versatile welding processes available today. This method is particularly advantageous for projects with strict budgets. It consistently incurs lower energy, labour, equipment, and tooling costs compared to other alternatives like vibration, hotplate, and laser welding.
By utilising high-frequency ultrasonic acoustic vibrations to create a solid-state weld, we can ensure reliable and robust joins in a wide array of materials. Additionally, ultrasonic welding is suitable for joining dissimilar materials, emphasizing its versatility and the ability to create strong bonds without adhesives.
The success of ultrasonic welding not only hinges on the equipment but also significantly depends on the design of the joint. Effective joint design requires careful attention to geometry, surface finish, and part thickness.
Selecting the appropriate joint configurations based on specific application requirements ensures that the welds are dependable and resilient. Attention to these details is critical for achieving optimal performance in ultrasonic welding.
In addition to design considerations, the choice of tools and machines plays a crucial role. By selecting the right ultrasonic welding machine, and ensuring proper setup and maintenance, we can enhance our manufacturing processes and achieve superior results.
This selection process often involves considering the size of the parts being welded and matching them with the appropriate frequency welding machine to ensure efficiency and effectiveness.
Key Takeaways
- Ultrasonic welding is cost-effective and versatile.
- Joint design is crucial for reliable welds.
- Choosing the right machine enhances manufacturing processes.
Fundamentals of Ultrasonic Welding
Ultrasonic welding is a precise method involving high-frequency vibrations, pressure, and energy to join materials. High frequency mechanical vibrations are applied to two materials to create heat through friction, which subsequently melts and fuses them together. This section breaks down the mechanics and main components involved in the process. The generator produces high frequency sound vibrations that are used to melt and bond thermoplastics, generating frictional heat at the joint area to enable the melting and bonding of thermoplastics.
Mechanics of Ultrasonic Welding and High Frequency Vibrations
Ultrasonic welding uses high-frequency ultrasonic vibrations to generate heat through friction. This heat is then used to bond materials together. The process starts when the generator converts electrical energy into high-frequency signals (usually around 20 kHz to 40 kHz).
These signals are sent to the converter, also known as the transducer. It transforms the electrical signals into mechanical vibrations. The booster then amplifies the amplitude of these vibrations. Finally, the vibrations pass through the welding stack to the materials, which are held together under pressure. This combination of high-frequency vibrations and pressure causes the materials to heat and bond.
The welding cycle is short, usually taking only a few seconds. This makes ultrasonic welding an efficient and fast method suitable for various applications, from automotive parts to consumer electronics. Our focus on optimising these mechanics ensures strong, reliable welds.
Components of Ultrasonic Welding Systems
Several key components make up an ultrasonic welding system: the generator, converter, booster, and welding stack.
- Generator: Converts electrical energy into high-frequency signals.
- Converter: Transforms electrical signals into mechanical vibrations.
- Booster: Amplifies the amplitude of the vibrations.
- Welding Stack: Directs these vibrations to the workpieces being welded.
The generator is pivotal as it starts the process by converting energy. The converter is just as crucial, changing this energy into vibrations. The booster ensures these vibrations are strong enough for the welding process. Lastly, the welding stack is the pathway for these vibrations to the materials, ensuring precise and effective welding.
Understanding these components helps us achieve efficient and high-quality welding results. This combination of high-frequency vibrations, mechanical precision, and strategic pressure application is what sets ultrasonic welding apart.
Ultrasonic Welding Machines
We will cover the main aspects of selecting, understanding, and operating an ultrasonic welder, emphasizing the importance of choosing the right machine. Our focus will be on ensuring quality, efficiency, and precision in your manufacturing processes.
Ultrasonic welders come with various specifications, including frequency ranges and power outputs, which are crucial for achieving reliable and efficient welding results.
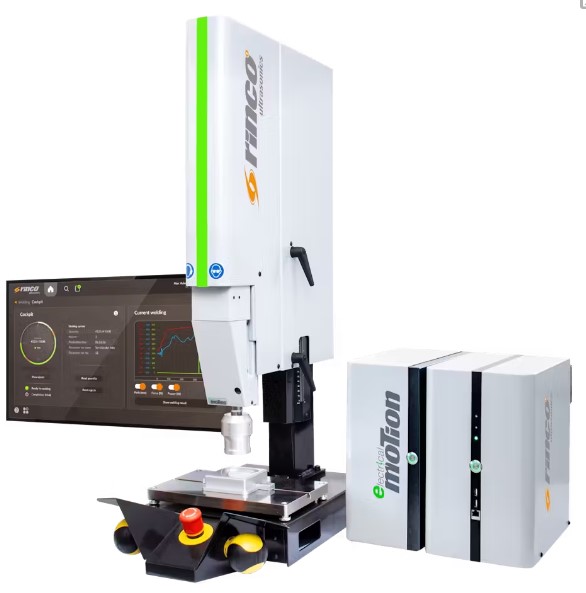
Choosing the Right Machine
Choosing the right ultrasonic welding machine is crucial for quality and efficiency. The first step is to consider the size of the parts being welded.
For large parts, a 20 kHz machine is ideal. Medium-sized parts usually require a 35 kHz machine, while small, delicate parts should use a 70 kHz machine.
Another important factor is the power range. Machines with higher power are suitable for tougher materials and larger parts. We must also look at machine press capabilities and cycle time to ensure they meet our production needs.
Part ejection features can further streamline the process by automatically removing completed parts, increasing throughput and reducing cycle times.
Understanding Machine Specifications
Understanding the specifications of ultrasonic welding machines is key to making an informed choice.
Resonant frequency is one of the most vital specs. The 15 kHz, 20 kHz, and 40 kHz options each serve different needs based on part size and material.
The power range indicates a machine’s ability to weld different materials. Higher power ranges are suited for high-melting temperature plastics.
Control and monitoring features ensure precision and quality. Many modern machines come with digital controls and Industry 4.0 integrations, which allow for better monitoring and adjustments to improve quality and reduce waste.
Machine Setup and Operation
Setting up and operating ultrasonic welding machines correctly ensures efficiency and high-quality results.
We start by assembling the machine according to the manufacturer’s guidelines. Proper alignment of the welding horn and fixture is critical.
During operation, monitoring the machine’s parameters like resonant frequency and power can help maintain consistency. Most machines have digital displays that show these metrics in real-time.
We should also schedule regular maintenance, including cleaning the horn and checking for wear, to keep the machine in top condition.
Training operators on machine use and safety protocols is essential. Skilled operators can adjust settings to optimise the welding process, ensuring the highest quality welds and reducing downtime.
Ultrasonic Tooling
In ultrasonic welding, tooling is essential to ensure precision, reliability, and stability. Effective tools like horns, sonotrodes, fixtures, and anvils play a crucial role in achieving high-quality welds. Custom tooling solutions can address specific application needs. Additionally, the use of a linear encoder is vital for precise measurements and control in advanced welding methods, particularly for implementing the ‘weld by distance’ technique.
Horn and Sonotrode Design
The horn, also called the sonotrode, is a critical component. It transforms ultrasonic vibrations into mechanical energy, facilitating the weld.
We ensure horns are designed with the right shape, material, and frequency to match the project’s requirements. Common materials include titanium, aluminium, and steel for their durability and acoustic properties.
Using the correct material and design reduces wear and enhances the performance, reliability, and lifespan of the ultrasonic welding process.
Fixture and Anvil Configuration
Fixtures and anvils are vital for holding the parts securely during welding. Correct configuration guarantees precise alignment and stable support, which are necessary for consistent weld quality.
Fixtures can be customised to fit various shapes and sizes, enhancing flexibility. We often utilise a dovetail head assembly for additional support, ensuring accuracy and stability.
Custom fixtures provide better support and improve the reliability of the process, reducing the likelihood of defects or misalignment.
Custom Tooling Solutions
Custom tooling solutions address unique project requirements. These solutions involve designing horns, fixtures, and anvils tailored to specific applications.
Our approach includes evaluating the needs for stability and precision. Custom tooling often incorporates advanced features like automated systems and specialised support structures to ensure optimal performance.
By tailoring tools to the specific needs of each project, we can provide solutions that enhance overall efficiency and weld quality. Custom solutions are crucial in handling complex or unique welding challenges, ensuring the best results for specialised applications.
Applications of Ultrasonic Welding
4.1 Applications of Ultrasonic Welding
In ultrasonic welding, high-frequency sound waves are utilised to join materials like plastics and metals efficiently. This technology is pivotal for industries that require strong, precise, and clean welds. Spot welding is particularly effective in joining thermoplastic materials at defined points without the need for pre-formed holes or energy directors, ensuring a strong bond formation.
4.2 Ultrasonic Welding in Medical Device Manufacturing
Thermoplastic welding, including ultrasonic welding, is extensively used in medical device manufacturing due to its ability to create strong molecular bonds through applied heat and pressure. This method ensures the production of reliable and durable medical components.
Automotive and Aerospace Industries
Ultrasonic welding is crucial in the automotive and aerospace industries for fastening together plastic components. The method ensures precision and durability, which are critical in these sectors.
For instance, this technique is used to assemble dashboards, door panels, and other interior components without the need for adhesives or fasteners. By providing a hermetic seal, ultrasonic welding ensures components are protected against moisture and contaminants.
In the aerospace industry, lightweight thermoplastic materials are often welded to reduce vehicle weight while maintaining strength. This contributes to better fuel efficiency and performance.
Medical Device Manufacturing
We see extensive use of ultrasonic welding in manufacturing medical products. This method enables the production of sterile and durable devices such as catheters, filters, and IV tube connectors.
Given the need for hygiene and precision, ultrasonic welding is perfect because it creates clean welds without adding contaminants. The technology also allows for bonding different kinds of thermoplastic materials, which is often needed in complex medical devices.
Another significant advantage is the speed of the process. Rapid welding results in high production rates, which is essential in meeting the ever-growing demand for medical devices.
Consumer Electronics
In the consumer electronics industry, ultrasonic welding is employed to assemble items such as smartphones, tablets, and wearables. The process ensures a strong and precise bond, which is vital for the integrity of electronics.
This technology doesn’t involve heat that could damage sensitive electronic components. Instead, it uses mechanical vibrations to generate the necessary heat to melt and join materials, safeguarding delicate circuits from harm.
Furthermore, ultrasonic welding is ideal for creating waterproof and dustproof seals around electronic housings, thereby enhancing the durability and lifespan of devices. These features are particularly valuable in consumer products that are frequently exposed to varying environmental conditions.
Material Considerations in Ultrasonic Welding
When working with ultrasonic welding, it’s crucial to understand the materials you’re using. This includes selecting compatible materials and designing joints properly to ensure a strong weld. Ultrasonic welding eliminates the need for mechanical fasteners, providing a clean and efficient assembly process.
Ultrasonic bonding is essential when discussing the design and configuration of joints, especially in the textile and nonwoven industries.
Material Selection, Compatibility, and Dissimilar Materials
Choosing the right materials is essential in ultrasonic welding. Generally, we work with thermoplastics because they melt and solidify easily.
Rigid materials transmit high-frequency vibrations better than flexible ones, making them more suitable for this process.
Polymer choice impacts the weld quality significantly. Not all polymers are compatible with each other, so selecting compatible materials is key.
When materials with different melting points are used, it can lead to an uneven weld. For best results, select materials that melt uniformly and solidify gradually.
Common polymers used include:
- Polypropylene (PP)
- Acrylonitrile butadiene styrene (ABS)
- Polycarbonate (PC)
Avoid using adhesives or other binding agents as they can interfere with the welding process.
Joint Design and Configuration
Joint design is another critical factor. Properly designed joints ensure the weld’s strength and durability. Common joint types include the shear joint, step joint, and tongue and groove joint, each serving different purposes.
A successful joint design considers the following:
- Contact Area: Sufficient contact area improves heat generation and weld strength.
- Horn and Tooling: The horn transfers ultrasonic energy into the materials. Its design must match the joint configuration.
- Preload and Pressure: Adequate pressure ensures the materials remain in contact during vibration.
We must pay attention to joint geometry to ensure it supports the process. By carefully planning the joint design, we can avoid failures and maximise the efficiency of our ultrasonic welding projects.
Quality and Testing
Ensuring the quality of ultrasonic welding involves thorough testing to assess weld strength and detect any defects. Process control is crucial in this context, as it ensures consistent quality and traceability by managing settings and operations in welding machines. Here’s a detailed look at the key aspects of quality and testing in ultrasonic welding.
Assessing Weld Strength and Integrity
Assessing weld strength and integrity is crucial to ensure high-quality welds. We focus on tensile testing to measure the force required to pull the welded components apart. This helps us determine the weld’s strength.
Another method we use is ultrasonic scanning, which detects internal defects or inconsistencies. Visual inspections also play an important role in assessing the aesthetic quality of the weld.
Combining these methods gives us a holistic view of the weld quality.
We conduct feasibility studies before mass production to understand potential challenges. These preliminary tests help fine-tune the welding parameters for optimal results. Detecting and correcting defects at this stage ensures a reliable production process.
Advantages and Limitations of Testing Methods
Each testing method has its advantages and limitations.
Tensile testing is highly accurate and provides quantitative data on weld strength, making it essential for critical applications. However, it requires specialised equipment and is time-consuming.
Advancements in Ultrasonic Welding
In recent years, ultrasonic welding has seen significant advancements. These include improved welding technology, more efficient processes, and the integration of digital controls to enhance precision and reliability. Ultrasonic vibration plays a critical role in generating the necessary heat for bonding materials, as it creates friction at the interface of the materials, allowing them to melt and fuse into a single assembly.
Innovation in Welding Technology
The landscape of ultrasonic welding is constantly evolving.
We’ve seen innovations such as linear encoders that provide precise measurements of welding parameters. This ensures consistent quality and reduces the likelihood of errors during the welding process.
Moreover, advancements in ultrasonic generators now allow for more efficient conversion of electrical energy into mechanical vibrations. This improves energy utilisation and enhances the overall welding strength. Another notable innovation is the development of multi-head welding systems.
These systems enable simultaneous welding of multiple points, vastly improving productivity in industrial applications. Additionally, the integration of Industry 4.0 technologies, such as real-time monitoring and data analytics, has significantly enhanced the operational efficiency of ultrasonic welding machines.
Trends in Ultrasonic Welding Processes
Several trends are shaping the future of ultrasonic welding.
One key trend is the growing adoption of digital controls and automation. These technologies allow for more precise control over welding parameters, leading to higher quality welds. Automation also reduces the need for manual intervention, increasing productivity.
The use of advanced materials in welding processes is another trend. We see a rise in the welding of thermoplastic composites, which offer superior bonding strength and are more cost-effective.
Further, there has been a shift towards environmentally friendly practices.
The industry is moving away from traditional adhesive and mechanical methods towards more sustainable solutions like ultrasonic welding. This not only minimises waste but also reduces the environmental impact.
Finally, the implementation of vibration welding techniques has improved the bond strength and durability of welded joints, making them suitable for more demanding applications.
Operational Considerations
When operating ultrasonic welding machines, it is vital to focus on safety, efficiency, and maintaining the equipment to ensure long-term reliability and cost-effectiveness.
Safe Operation Practices
We must prioritise safety when using ultrasonic welding machines.
Always ensure that operators receive proper training and are aware of the machine’s components and functions. Personal protective equipment (PPE) such as gloves and safety glasses should be worn at all times.
Regularly inspect the machine for any wear or damage. Keep the work area clean to prevent any hazardous situations.
It is important to follow all manufacturer guidelines and safety protocols, including the correct use of cooling systems to prevent overheating.
In case of any malfunction, turn off the machine immediately and consult the operation manual or a qualified technician. A written safety plan, including emergency procedures, should be accessible to all staff.
Maximising Efficiency and Throughput
To maximise efficiency and throughput, we must ensure that ultrasonic welding machines are set up correctly.
This includes choosing the right frequency based on the size of the parts. For instance, 15 kHz machines are suited for large parts, while 40 kHz machines are better for small, delicate parts.
Regular calibration and adjustments help maintain optimal performance. Automated systems can be utilised to increase precision and reduce human error.
We should also consider the arrangement of the workspace to minimise movement and idle time.
By streamlining processes and using proper tooling, we can significantly enhance production speed. Keeping a close eye on machine settings ensures consistent quality and minimal rework.
Maintaining Ultrasonic Welding Equipment
Proper maintenance is crucial for the reliability of ultrasonic welding machines.
Routine checks and cleaning are necessary to prevent issues that could slow down production or cause costly repairs.
Make sure to inspect components like the ultrasonic horn, booster, and transducer regularly.
Lubricate moving parts as recommended by the manufacturer.
It is also essential to ensure that cooling systems are functioning correctly to prevent overheating, which can lead to equipment failure.
Maintaining detailed maintenance logs can help track the condition of the machinery and predict potential failures. Scheduled downtime for maintenance can prevent unexpected breakdowns and extend the lifespan of the equipment.
Economic and Environmental Impact
Ultrasonic welding is both cost-effective and environmentally friendly. By reducing costs and fostering sustainability, this technology offers significant advantages over traditional methods.
Cost Analysis and Reduction Strategies
Ultrasonic welding is highly cost-effective.
The initial investment in the machinery might seem high, but the long-term savings are substantial.
Energy consumption is lower compared to other processes like hotplate or laser welding.
Additionally, labour costs are reduced due to automation and shorter cycle times.
Notably, the tooling costs are low, and tools have a long lifespan.
Moreover, lead times for production are shorter, meaning businesses can respond quickly to market demands.
This versatility makes ultrasonic welding ideal for mass production where both time and cost savings are crucial.
Environmental Considerations
Ultrasonic welding has a positive environmental impact.
Unlike traditional welding methods, ultrasonic welding does not generate harmful fumes or gases. This vastly improves air quality in the workplace, ensuring a healthier environment for workers.
The process eliminates the need for adhesives or solvents, reducing the release of toxic substances into the environment.
We can cut down on waste and improve sustainability across various industries.
Ultrasonic welding also contributes to energy conservation due to its efficiency, making it a preferable option in our push towards a sustainable future.
Frequently Asked Questions
Below, we address various questions about the operation, challenges, and safety of using ultrasonic welding machines. This guide covers principles, material influences, weld joint design, and common issues.
What principles govern the operation of ultrasonic welding machines?
Ultrasonic welding machines use high-frequency vibrations to create heat through friction. This energy melts materials at the joining surface, allowing them to fuse together quickly. The primary components include a power supply, a transducer, and a welding tool that directs the vibrations onto the materials.
What is the primary challenge encountered in ultrasonic welding processes?
The main challenge in ultrasonic welding is ensuring proper joint design.
Effective welding requires precise geometry, surface finish, and material thickness.
Poor joint design can result in weak welds or inconsistencies, affecting the final product’s reliability.
Could you explain the basic concepts underlying ultrasonic welding?
Ultrasonic welding employs high-energy vibrations to bond materials.
Introduced in 1961, it uses sound waves to generate frictional heat.
These sound waves cause the materials to melt at their interface, leading to a strong, permanent bond upon cooling.
What is considered a significant drawback of using ultrasonic welding equipment?
A significant drawback is its limitation with certain materials and thicknesses.
Ultrasonic welding is most effective with thin, rigid plastics. It may not work well with thicker or more flexible materials, limiting its application in some industrial processes.
How do the material properties influence the ultrasonic welding procedure?
Material properties such as density, elasticity, and melting point significantly affect the welding outcomes.
Denser materials may require more energy, while more elastic materials might absorb vibrations differently, impacting weld strength.
Selecting suitable materials is crucial for achieving strong, reliable bonds.
What safety precautions are recommended when operating ultrasonic welding machinery?
Operators should wear appropriate personal protective equipment. This includes ear protection to guard against high-frequency noise.
It is also essential to ensure that the machinery is correctly grounded. Also, make sure that all connections are secure to prevent electric shocks and mechanical failures.
Regular maintenance checks can help in mitigating risks.