Ultrasonic welding has revolutionised the medical industry by providing a clean, efficient, and reliable method for joining plastic parts. This technique uses high-frequency vibrations to create frictional heat, melting the materials at the joint and forming a strong bond. The medical industry favours ultrasonic welding because it eliminates the need for harsh chemicals or adhesives, ensuring biocompatibility and safety.
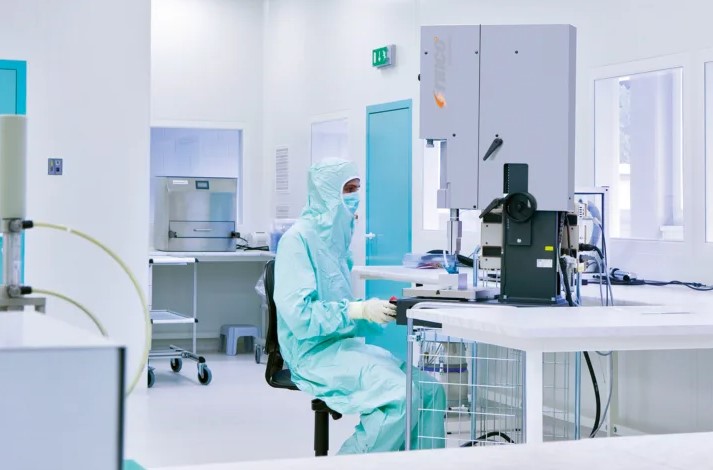
The process is particularly useful for creating medical devices that require sterile and precise assembly. From intricate tools to disposable products, ultrasonic welding delivers repeated, consistent results. By investing in this technology, manufacturers can ensure their products meet stringent regulatory standards and maintain high quality.
Ultrasonic welding also supports advanced manufacturing capabilities, including the use of cleanrooms and process monitoring for traceability. As the medical industry continues to evolve, this technology will play a crucial role in developing new devices and applications, keeping us at the forefront of innovation.
Key Takeaways
- Ultrasonic welding ensures biocompatibility and safety in medical devices.
- It provides clean, efficient, and precise assembly of medical components.
- Advanced capabilities support regulatory compliance and high-quality manufacturing.
Overview of Ultrasonic Welding in the Medical Industry
Ultrasonic welding has become a crucial process in the medical industry due to its ability to create reliable bonds without using adhesives. This method is particularly suitable for medical devices, where cleanliness and precision are paramount.
Principles of Ultrasonic Welding
Ultrasonic welding utilises high-frequency vibrations to generate heat and bond materials. When ultrasonic energy is applied, it causes the materials to vibrate, producing friction at the interface. This friction generates heat, melting the materials and allowing them to fuse together. Key components include the ultrasonic horn, which transmits the vibrations, and the anvil, which holds the materials in place. The process is controlled by adjusting parameters like amplitude and pressure to ensure a strong weld.
Comparing Ultrasonic Welding to Other Joining Techniques
Compared to other methods like heat welding and the use of adhesives, ultrasonic welding offers several benefits. We don’t need chemical solvents or glues, which can be harmful and affect biocompatibility. Ultrasonic welding also produces consistent and repeatable results, crucial for medical device manufacturing. While other methods might require longer cooling times, ultrasonic welding is quick, often completing in seconds. This efficiency makes it particularly advantageous in high-volume production environments.
Key Components of Ultrasonic Welding Systems
Our ultrasonic welding systems consist of several main components. The power supply generates the ultrasonic energy, which is delivered to the transducer. The transducer converts this energy into mechanical vibrations. The booster amplifies these vibrations and passes them to the horn, which contacts the materials to be welded. Each component must be precisely calibrated to ensure optimal performance. Adjusting the amplitude, pressure, and duration allows for control over the welding process, ensuring that the final product meets strict medical standards.
Rinco Ultrasonic Plastic Welders
Rinco Ultrasonics is renowned for its advanced ultrasonic plastic welders, which are widely used in the medical industry. Their systems are designed to meet stringent medical standards, providing reliable and consistent welds. Rinco’s welders feature user-friendly interfaces and precise control over welding parameters like amplitude and pressure. These systems can handle a variety of thermoplastics, making them versatile for various medical applications. The cleanroom compatibility of Rinco ultrasonic welders ensures that our welding processes do not introduce contaminants, maintaining the integrity of medical devices.
Materials in Ultrasonic Welding for Medical Devices
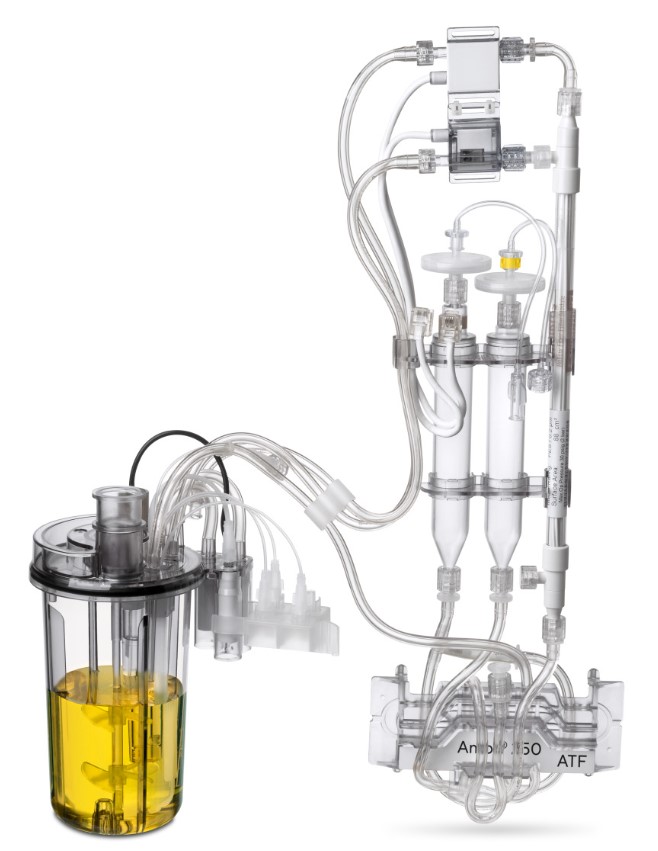
Understanding the different materials used in ultrasonic welding is crucial for the medical industry. We need materials that have the right properties, are biocompatible, and can withstand various chemical environments.
Common Thermoplastics Used
Thermoplastics are widely used in ultrasonic welding. Polypropylene (PP) and polyethylene (PE) are common choices due to their excellent weldability. Polycarbonate is also popular because of its strength and clarity.
PP is often used for medical containers and syringes. PE is favoured for tubing and flexible components. Polycarbonate is chosen for devices needing transparency, like housings for diagnostic equipment. These materials provide the durability and reliability essential for medical use.
Biocompatibility of Materials
Biocompatibility is a top priority in medical devices. Materials used must not cause any adverse reactions when in contact with human tissue. Thermoplastics such as PP, PE, and polycarbonate meet these requirements.
PP and PE are inert, which means they don’t react with biological tissues. Polycarbonate can also be biocompatible, making it suitable for components that come into direct contact with the body. This ensures safety and minimises any risk of complications for patients.
Material Properties and Chemical Resistance
The properties and chemical resistance of materials are crucial. PP and PE are known for their chemical resistance. They don’t react with most chemicals, making them ideal for medical applications where sterilisation and exposure to disinfectants are common.
Polycarbonate offers high impact resistance and can withstand repeated sterilisation cycles without degrading. This makes it suitable for reusable medical instruments. Each of these materials maintains its integrity under harsh conditions, ensuring the longevity and reliability of medical devices.
Medical Device Manufacturing with Ultrasonic Welding
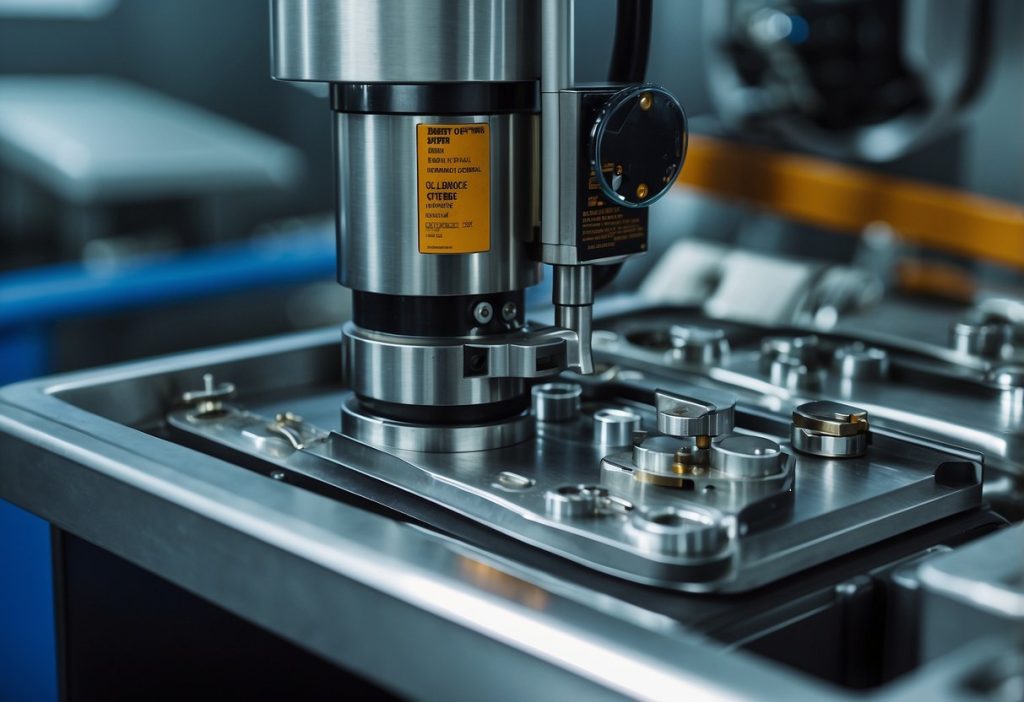
Ultrasonic welding plays a critical role in the medical device sector. This technique offers precise, repeatable welds required for high-quality standards in healthcare applications such as catheters and masks.
Applications in Medical Industry
Ultrasonic welding is used extensively in medical applications for joining plastic components. This method is preferred because it avoids the use of harsh chemicals or adhesives, ensuring biocompatibility. Common medical devices that benefit from ultrasonic welding include catheters, masks, and various disposables.
Ultrasonic welding is invaluable for producing items in cleanrooms. The process meets stringent hygiene standards because it does not introduce contaminants. By using ultrasonic vibrations to form bonds, we help maintain the integrity and safety of the medical devices we manufacture.
Regulations and Quality Standards
Meeting the highest quality standards is crucial in medical device manufacturing. Ultrasonic welding aligns well with these demands by offering precise and reliable bonds. Regulations often require that no harmful substances be introduced during the assembly process. Ultrasonic welding achieves this by avoiding chemical solvents.
Medical devices must comply with various international standards like ISO 13485. Ultrasonic welding helps us meet the biocompatibility requirements set forth by these standards. This ensures the safety and efficacy of the devices used in healthcare.
Joining Techniques and Effect on Device Performance
The joining techniques used in ultrasonic welding significantly affect the performance of medical devices. The process involves high-frequency vibrations applied to the parts being welded, generating heat at the joint and forming a bond. This method ensures strong, durable connections that are essential for medical applications.
By eliminating the need for adhesives or solvents, ultrasonic welding reduces the risk of chemical residue. This is particularly important for devices such as catheters, which come into direct contact with sensitive tissues. The consistent quality of welds produced via ultrasonic welding enhances the performance and reliability of medical devices, fulfilling critical needs in the healthcare industry.
Design Considerations for Ultrasonic Welding
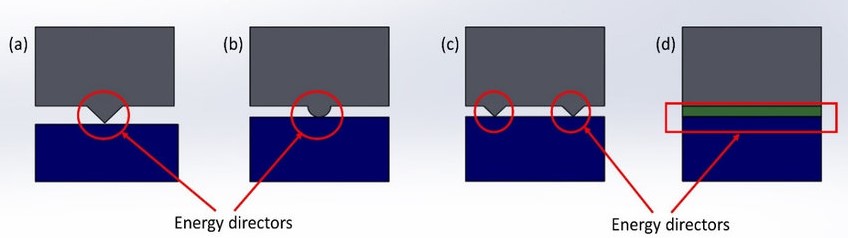
When designing for ultrasonic welding in the medical industry, several critical aspects must be addressed to ensure successful outcomes. Key considerations include part and joint design, manufacturing and assembly processes, and the role of the energy director.
Part Design and Joint Design
Part Design: The success of ultrasonic welding starts with well-thought-out part design. Parts need to be compatible with the ultrasonic process, which means choosing suitable materials that respond well to ultrasonic energy. Polymers that soften at the welding frequency are ideal.
Joint Design: Joint design is equally crucial. Different joint designs, such as shear joints, step joints, and butt joints, can be used based on the application. Optimising the joint geometry, ensuring good surface finish, and appropriate part thickness are important steps in achieving strong and reliable welds.
Design for Manufacturing and Assembly
Design for Manufacturing: We must consider the manufacturability of parts during the design phase. Each component should be designed to fit within the tolerances required for ultrasonic welding. Using precise dimensions reduces the need for rework and ensures consistency in production.
Design for Assembly: The design should also facilitate easy assembly. This includes designing parts that fit together seamlessly, ensuring alignment features, and considering how parts will be held in place during welding. Using appropriate fixtures can help maintain part alignment and stability during the welding process.
Energy Director and Its Role
Energy Director: An energy director is a small, triangular ridge moulded into the part at the joint interface. Its purpose is to focus the ultrasonic energy at the point where welding is to occur. This ensures efficient heat generation and a strong weld.
Role of Energy Director: The design of the energy director involves choosing the right size and shape depending on the materials and joint design. It plays a crucial role in achieving a consistent and strong weld by concentrating the ultrasonic energy precisely where it is needed. This leads to better control over the welding process and improved joint quality.
The considerations outlined are essential in designing effective ultrasonic welding processes for medical devices, ensuring high-quality and reliable outcomes.
Process Parameters and Control in Ultrasonic Welding
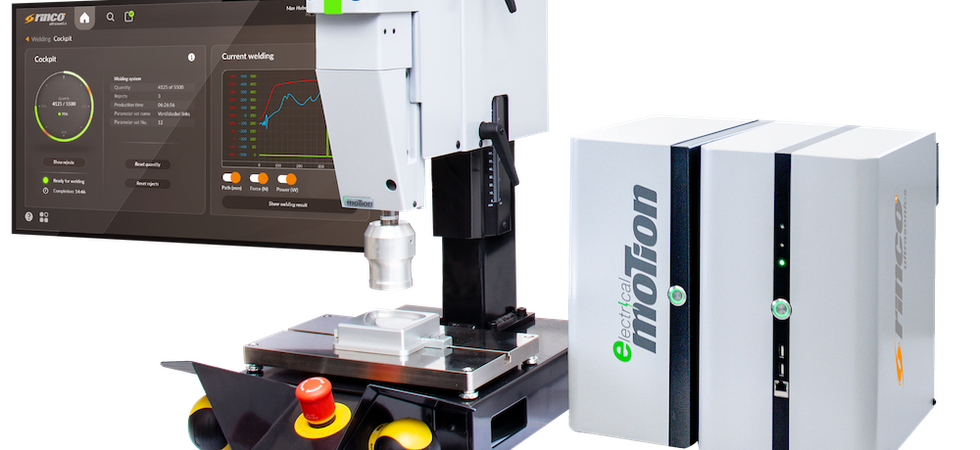
In ultrasonic welding for the medical industry, precise control of process parameters is essential to ensure high weld quality and strength. We will explore key factors such as optimising weld parameters, maintaining process control, and troubleshooting common issues.
Optimising Weld Parameters for Quality
To achieve high-quality welds, we must fine-tune several parameters. Key factors include vibration amplitude, welding time, welding force, and energy levels.
Vibration amplitude, typically measured in microns, affects the degree of ultrasonic energy transferred to the materials. Higher amplitudes may result in stronger welds but can lead to material damage if not controlled.
Welding time is crucial as it determines how long the materials are exposed to ultrasonic energy. Too short a time can result in weak welds, while too long a time can degrade the material.
Welding force or pressure must be balanced to avoid insufficient contact between materials or excessive pressure that could cause deformation.
By adjusting and monitoring these parameters meticulously, we can achieve reliable and repeatable welds suitable for sensitive medical applications.
Process Control and Validation
Ensuring process control in ultrasonic welding involves real-time monitoring and validation.
We deploy sensors and control systems to track parameters like amplitude, force, and time during each weld cycle. Advanced systems use feedback loops to adjust parameters dynamically, maintaining consistency across batches.
Validation ensures the process meets regulatory standards. This includes recording weld data and performing mechanical tests to verify weld strength and reliability.
Process control is also about documenting every step, from initial setup to final validation. This documentation supports regulatory compliance and enables traceability, ensuring our medical devices meet the highest quality standards.
Troubleshooting Common Welding Issues
Despite careful control, issues can arise in ultrasonic welding. Common problems include misaligned joints, weak welds, and material degradation.
Misalignment often results from improper fixture design or setup. To prevent this, we must ensure fixtures hold components securely and in the correct position.
Weak welds can arise from incorrect parameter settings. Revisiting welding force, time, and amplitude settings can often address this issue.
Material degradation is typically due to excessive energy or pressure. Reducing amplitude or adjusting weld time can mitigate this problem.
By systematically addressing these issues, we maintain the integrity and quality of our ultrasonic welding processes, crucial for producing safe and effective medical devices.
Ultrasonic Welding in Assembly Operations
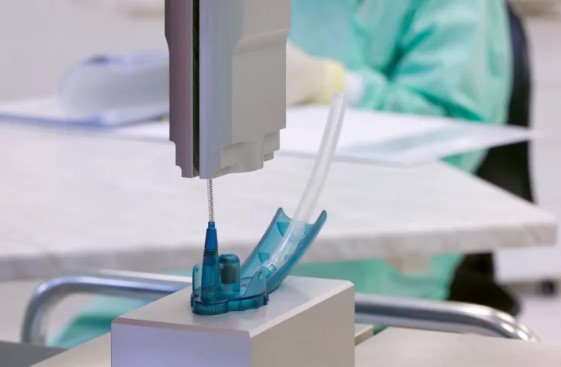
Incorporating ultrasonic welding into assembly operations offers precise, reliable joining methods suitable for large-scale production. Key aspects include seamless integration into automated lines, advanced fixture and part handling systems, and consistency in weld quality.
Integration into Automated Production Lines
Ultrasonic welding fits well into automated production lines, enhancing efficiency and precision. By using robotics and computer-controlled systems, we can automate the welding process. This reduces human error and ensures consistent results.
The short cycle time of ultrasonic welding is crucial for high-volume production. It minimises downtime and keeps our production schedules on track. We can also adapt the equipment to different applications, making it versatile for various needs in medical assembly.
Automation lowers labour costs and streamlines the production process. We deploy sensors and monitors to ensure each weld meets strict quality standards, vital in medical manufacturing.
Fixture and Part Handling Systems
Effective fixture and part handling systems are essential for ultrasonic welding. These systems hold components in place with high precision, ensuring accurate and repeatable welds. We use custom-designed fixtures tailored to the specific parts being joined.
Part handling systems move components through the welding process smoothly. Automated conveyance systems, such as robots or conveyors, are integrated to position parts correctly under the welding horn. This automation enhances throughput and reduces manual handling errors.
Additionally, we ensure fixtures are robust and capable of withstanding the ultrasonic vibrations. Proper part alignment is critical to achieving strong and reliable welds, especially in sensitive medical devices.
Ensuring Consistency and Reliability
Consistency and reliability are paramount in ultrasonic welding for medical assembly. We employ stringent quality control measures throughout the production process. Automated systems are equipped with sensors to monitor each weld’s parameters, such as amplitude, force, and time.
We regularly calibrate equipment to ensure it operates within specified tolerances. Data from the welding process is logged and analysed to identify any deviations from standards. This helps in maintaining high-quality welds consistently.
Reliability is enhanced through thorough testing. We conduct destructive and non-destructive tests to verify the strength and integrity of welds. This rigorous testing ensures that our welding processes meet the stringent requirements of the medical industry.
Environmental and Safety Considerations
When using ultrasonic welding in the medical industry, it is crucial to be mindful of environmental sustainability and the safety of operators. We must focus on reducing waste and ensuring that operators work in a safe environment without compromising their health.
Waste Reduction and Sustainability
Ultrasonic welding is noted for being environmentally friendly because it reduces the need for chemical solvents and adhesives. These chemicals can be hazardous, require special disposal, and contribute to environmental pollution. By eliminating them, we not only create a safer product but also lessen our ecological footprint.
Another key aspect is that ultrasonic welding generates very little waste. Since the process involves precise and localised heating, there is minimal material loss. This efficiency is especially important when working with costly or limited materials.
Sustainability is further enhanced because ultrasonic systems have long lifespans and require less maintenance compared to other methods. This reduces the frequency of equipment replacement and disposal, contributing to overall sustainability initiatives within the medical industry.
Ensuring Safety for Operators
For operators, safety is paramount. Ultrasonic welding significantly reduces exposure to harmful chemicals that can cause respiratory and skin issues. This is crucial for maintaining a healthy workforce.
We must also ensure that workplaces are ergonomically designed to support operators. The equipment should be easy to use, reducing the risk of repetitive strain injuries. Implementing proper training programmes is essential so that everyone understands how to operate the machinery safely and effectively.
Noise reduction is another safety consideration. Ultrasonic welding machines operate at high frequencies but should be equipped with sound-dampening features. This lowers the risk of hearing damage, making the workplace safer and more pleasant for operators.
By focusing on waste reduction and operator safety, we uphold both environmental and health standards, which are critical in the medical industry.
Future Trends in Ultrasonic Welding
As we look ahead, several trends are poised to shape the future of ultrasonic welding in the medical industry.
Diagnostic Precision
We expect advancements in ultrasonic welding to enhance the precision of diagnostic device manufacturing. Tighter welds and improved quality control will drive more reliable diagnostic tools, essential for accurate patient care.
Sustainability Initiatives
Sustainability is increasingly important. Ultrasonic welding uses less energy compared to traditional methods like laser welding, making it a more environmentally friendly choice. This shift towards greener practices aligns with global sustainability goals.
Innovation in Materials
Innovation continues with the development of new materials compatible with ultrasonic welding. For example, the welding of BPA-free plastics ensures compliance with strict health regulations.
Market Adaptations
The medical industry demands high standards. New ultrasonic welding technologies are emerging to meet these requirements, particularly in cleanroom settings where contamination is a critical concern. These innovations help maintain the integrity of sensitive medical devices.
Regulatory Changes
Possible bans on certain harmful substances, such as specific adhesives, will likely increase reliance on ultrasonic welding. This method offers a cleaner, safer alternative, particularly in medical applications requiring non-toxic components.
Increased Adoption
We’re likely to see broader adoption of ultrasonic welding as it becomes more integrated into medical device manufacturing. Companies are investing in this technology to stay ahead of regulatory changes and market demands.
In conclusion, the future of ultrasonic welding in the medical industry looks promising with a strong focus on precision, sustainability, and innovation. This trend is set to revolutionise how we approach medical device manufacturing, driving efficiency and compliance across the board.
Frequently Asked Questions
In this section, we’ll address common questions about ultrasonic welding in the medical industry. We will cover its benefits, material compatibility, cost implications, and technological advancements.
What are the benefits of using ultrasonic welding for medical device assembly?
Ultrasonic welding offers a fast, clean, and efficient way to join plastic parts. It does not introduce glues or adhesives into the device, making it ideal for medical applications. The process is repeatable and ensures a strong, reliable bond.
How does ultrasonic welding ensure sterility in medical products?
The ultrasonic welding process generates heat through high-frequency vibrations, which can help maintain the sterility of medical products. By avoiding the use of adhesives or other chemicals, ultrasonic welding reduces the risk of contamination, ensuring that assembled products meet strict hygiene standards.
What types of materials can be joined using ultrasonic welding in the medical field?
Many thermoplastics, both amorphous (such as polystyrene) and semi-crystalline (such as nylon), can be joined using ultrasonic welding. Ideally, the parts to be welded are made from the same material to achieve the best results. This technology is widely used for various plastic components in medical devices.
What are the cost implications of implementing ultrasonic welding in medical manufacturing?
Implementing ultrasonic welding can involve initial costs for the equipment and tooling. However, the long-term savings from increased production speeds, reduced labour costs, and improved product reliability can outweigh these initial expenses. This makes ultrasonic welding a cost-effective solution over time for medical manufacturing.
How does ultrasonic welding compare to traditional bonding methods for medical components?
Compared to traditional bonding methods such as gluing or screwing, ultrasonic welding is faster and cleaner. It forms strong, permanent bonds without the need for additional materials, reducing the risk of contaminants. This is particularly important in the medical field where product reliability and cleanliness are critical.
What advancements in ultrasonic welding technology can be expected to impact the medical industry?
Future advancements in ultrasonic welding technology may include improved precision and control, allowing for the welding of even more complex and intricate designs. Enhanced tooling and automation capabilities are also likely, which could further increase production efficiency and consistency in medical device manufacturing.